Contrôle d’étanchéité
Une fuite est définie comme le passage d’un fluide ou d’un gaz par exemple, au travers d’une fissure s’étant établie dans une paroi ayant une certaine épaisseur. Cette fissure est généralement complexe, elle ne suit pas une ligne droite et peut avoir une largeur évolutive entre son commencement d’un côté et sa fin de l’autre.
Une fuite ne pourra techniquement pas exister s’il n’existait pas une différence de pression de part et d’autre de la paroi « fissurée ». Cette pression peut être le poids d’un liquide statique ou la pression d’un gaz comprimé ne demandant qu’à s’échapper dans l’atmosphère. Une fuite est donc toujours de la zone de plus forte pression vers celle de moindre pression.
Pour quantifier une fuite, on parlera de son flux de fuite, défini par la formule suivante :

Il est ainsi possible de calculer des flux de fuite acceptables, également appelés seuil de rejet dans le cadre d’un test, et ce sur une période de temps donné associé à une perte acceptable.
Un système de test d’étanchéité par gaz traceur He, H2, … comporte entre autres :
1. Un gaz traceur : l’hélium ou l’hydrogène sont tous les deux employés. L’hélium peut être employé pur pour plus de sensibilité ou dilué dans un souci d’économie. L’hydrogène quant à lui ne sera utilisé comme traceur que sous une forme diluée, typiquement dans de l’azote, à hauteur de 5% (5% H2 95% N2). L’hydrogène sera limité aux tests par reniflage dans l’atmosphère (voir ci-après), étant donné que sous vide, beaucoup de matériaux dégazent de l’hydrogène, parasitant ainsi la mesure.
2. Un détecteur de fuite : indispensable, c’est un spectromètre de masse travaillant sous vide. La cellule d’analyse est calibrée pour détecter et quantifier précisément l’hélium ou l’hydrogène s’échappant des produits testés.
3. Des pompes ou groupes de pompes à vide : que ce soit pour un test sous vide ou du reniflage, les produits à tester seront évacués à l’aide d’une pompe primaire avant de les pressuriser. De même, la chambre à vide dans le cadre d’un test global (voir ci-après) devra être évacuée jusqu’à par exemple 10-2 ou 10-3 mbar pour une sensibilité de l’ordre de 10-6 atm.cm3/s.
4. Un bâti : selon vos besoins, composé d’un châssis mécano-soudé, de panneaux de protection en polycarbonate, de profilés aluminium. C’est le support pour la chambre de test où vos pièces seront testées. Il permet aussi de supporter les autres organes comme les groupes de pompes à vide, l’armoire électrique etc.
5. Interface opérateur : pour une gestion optimale du système, un écran tactile pour commander l’automatisme de la machine, un écran plat additionnel pour visualiser les courbes du cycle de test (pression, temps de test…), une colonne lumineuse à LED pour une utilisation en production… Toutes les configurations sont possibles.
Test global
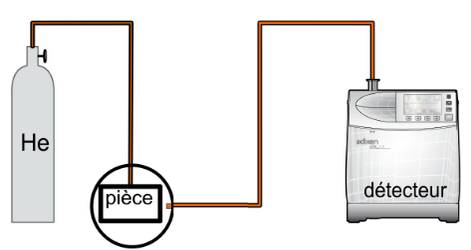
- La pièce est placée dans une chambre à vide
- Le détecteur est connecté à la chambre
- La chambre est évacuée
- La pièce est vidée de son air puis pressurisée à l’hélium
- L’hélium s’échappe de la pièce et est quantifié par le détecteur
Test par reniflage
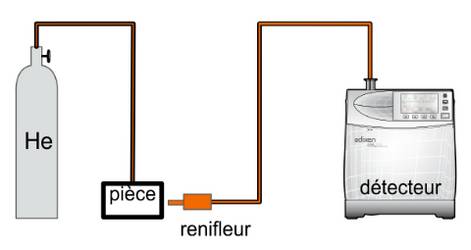
- Aucune chambre à vide n’est nécessaire
- La pièce est pressurisée à l’hélium
- La sonde de reniflage est reliée au détecteur de fuite
- Un opérateur passe la sonde autour de la pièce jusqu’à détection de la fuite
Test par aspersion

- La pièce est pompée par le détecteur lui-même ou une pompe en parallèle
- Le détecteur est donc connecté à la pièce à tester
- L’opérateur asperge d’hélium par à-coups les zones pouvant abriter une fuite
- L’hélium rentre par la fissure et est quantifié par le détecteur